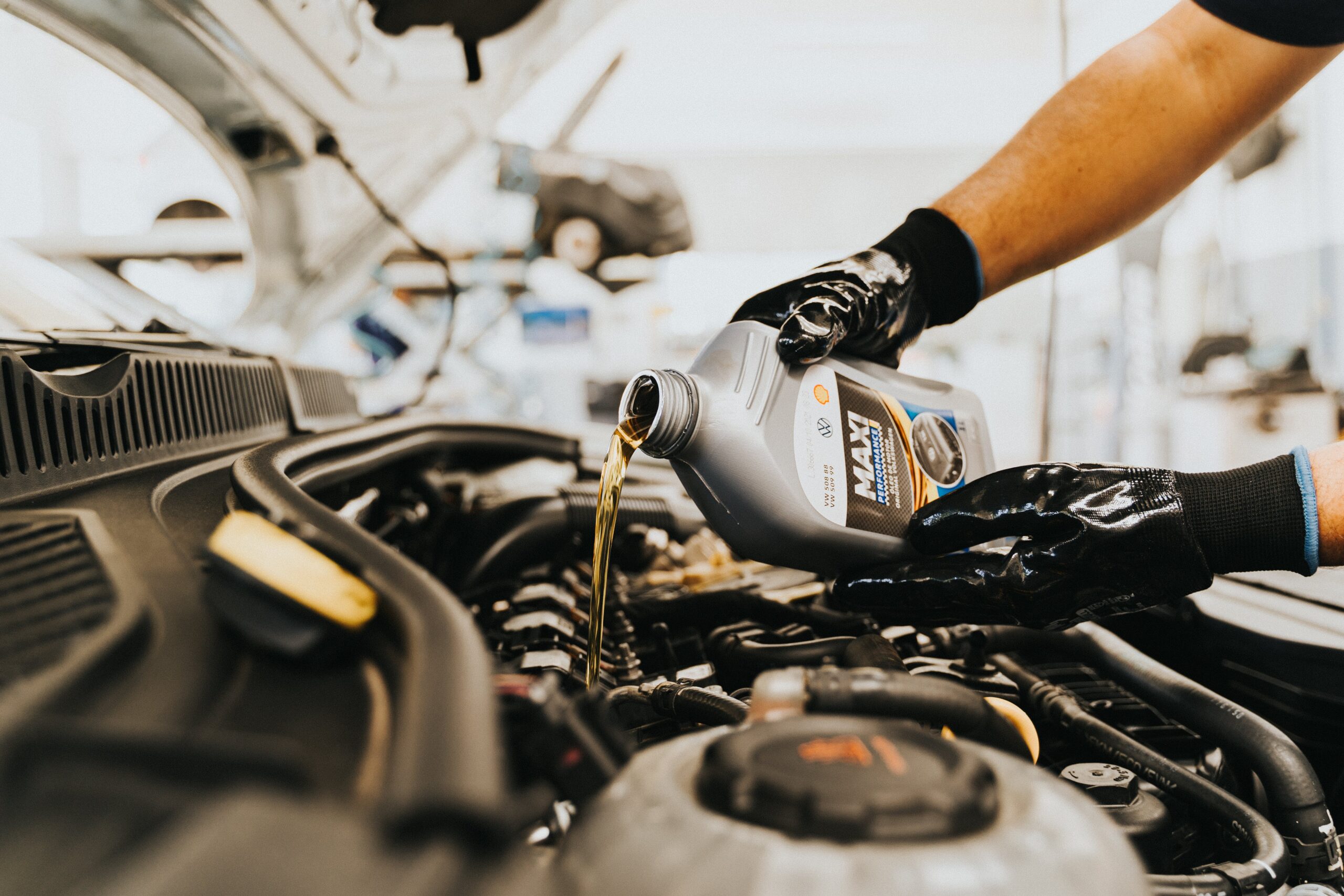
Abstract
Diesel Engine Manufacturers provide engines to various Original Equipment Manufacturers (OEMs) in the commercial vehicles sector, specifically trucks and buses. The Diesel Engine Management (DEM) web application was conceptualized as part of a two-week case study for BOSCH. Its purpose was to enable diesel engine manufacturers to monitor and track the service and maintenance of engines and engine parts supplied to OEMs and subsequently, their end customers. The application was designed for use by multiple parties within the diesel engine ecosystem: manufacturers and technicians on one side, and dealers and customers on the other.
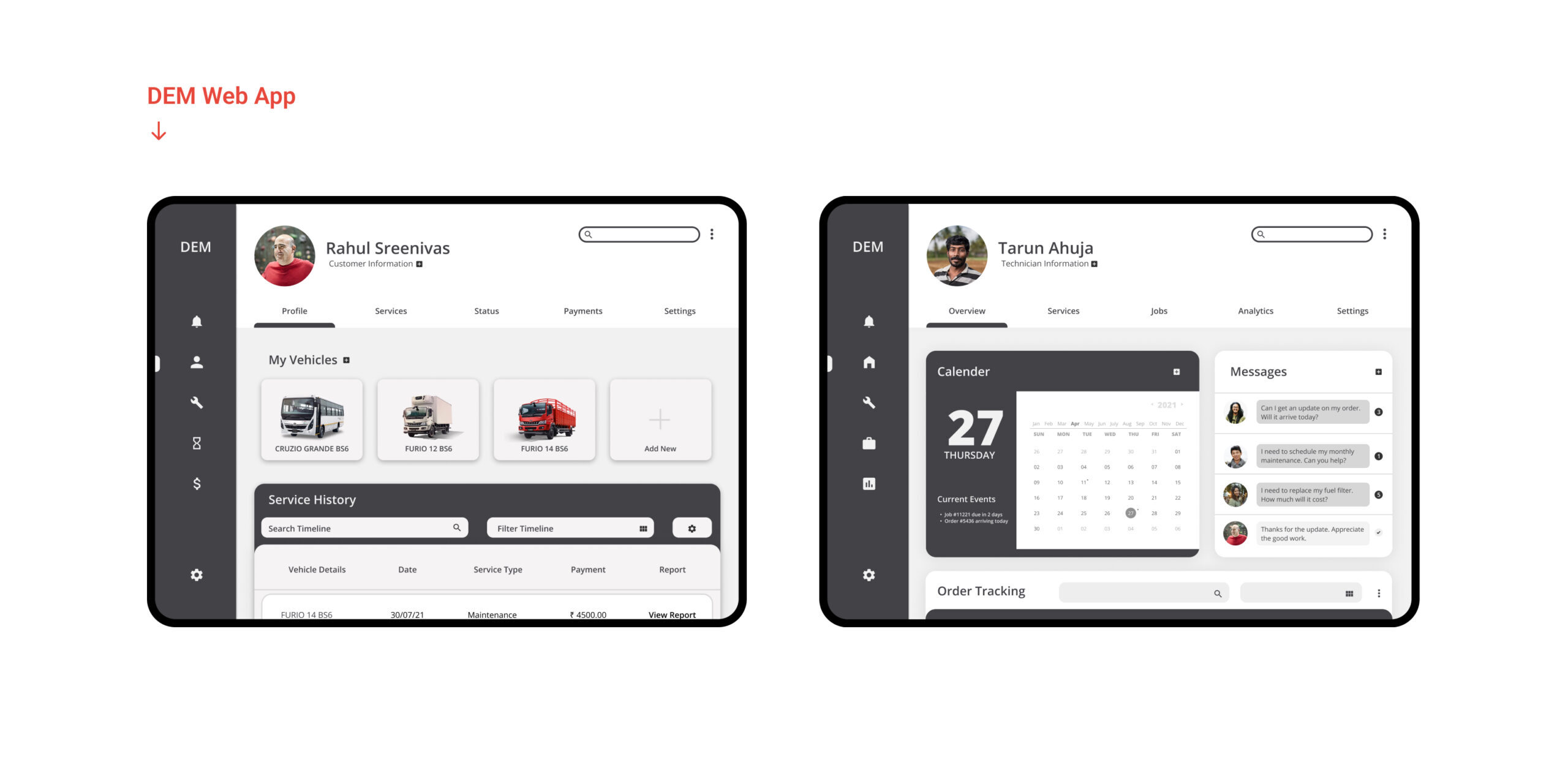
The web application functioned as a customizable dashboard tailored to the needs of different user types. Two versions were developed: a technician dashboard and a customer dashboard, each offering specific tasks and features relevant to their respective user roles.
Qualitative Research
The main objective of the research process was to achieve a thorough understanding of the diesel engine landscape. This involved identifying the diverse stakeholders and user groups, mapping out the automotive supply chain and process streams, evaluating the existing frameworks employed by different diesel engine manufacturers, and gathering insights on service gaps and potential opportunities. These insights were derived from firsthand accounts provided by industry experts, users, and agents involved in the field, and were further validated through secondary research.
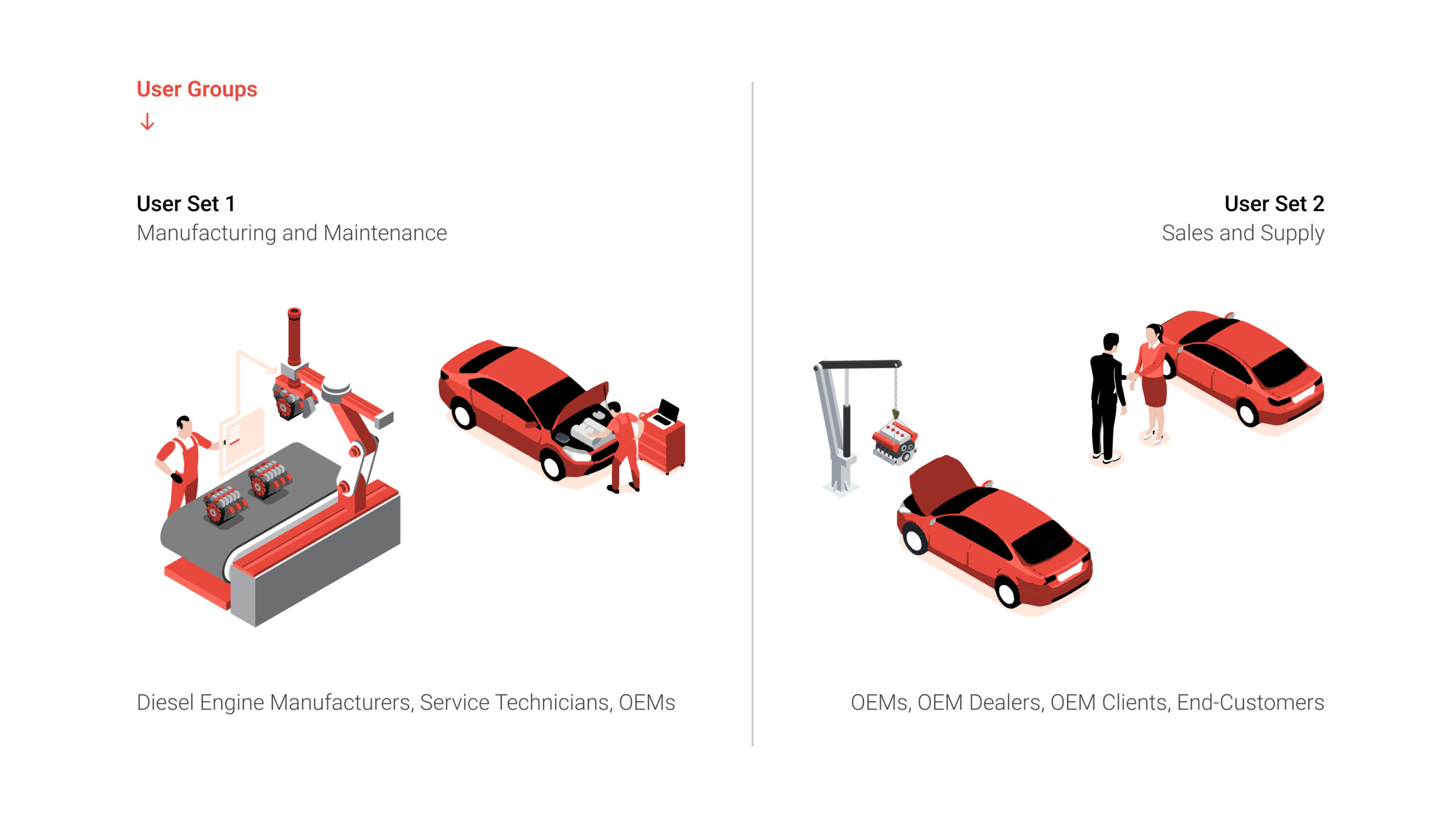
A plethora of stakeholders and key players were recognized within the diesel engine ecosystem. However, for simplicity, they could be broadly categorized into two user sets. The first set is associated with the engine itself, while the second set pertains to the engine’s journey as it transitions into the automotive sector.
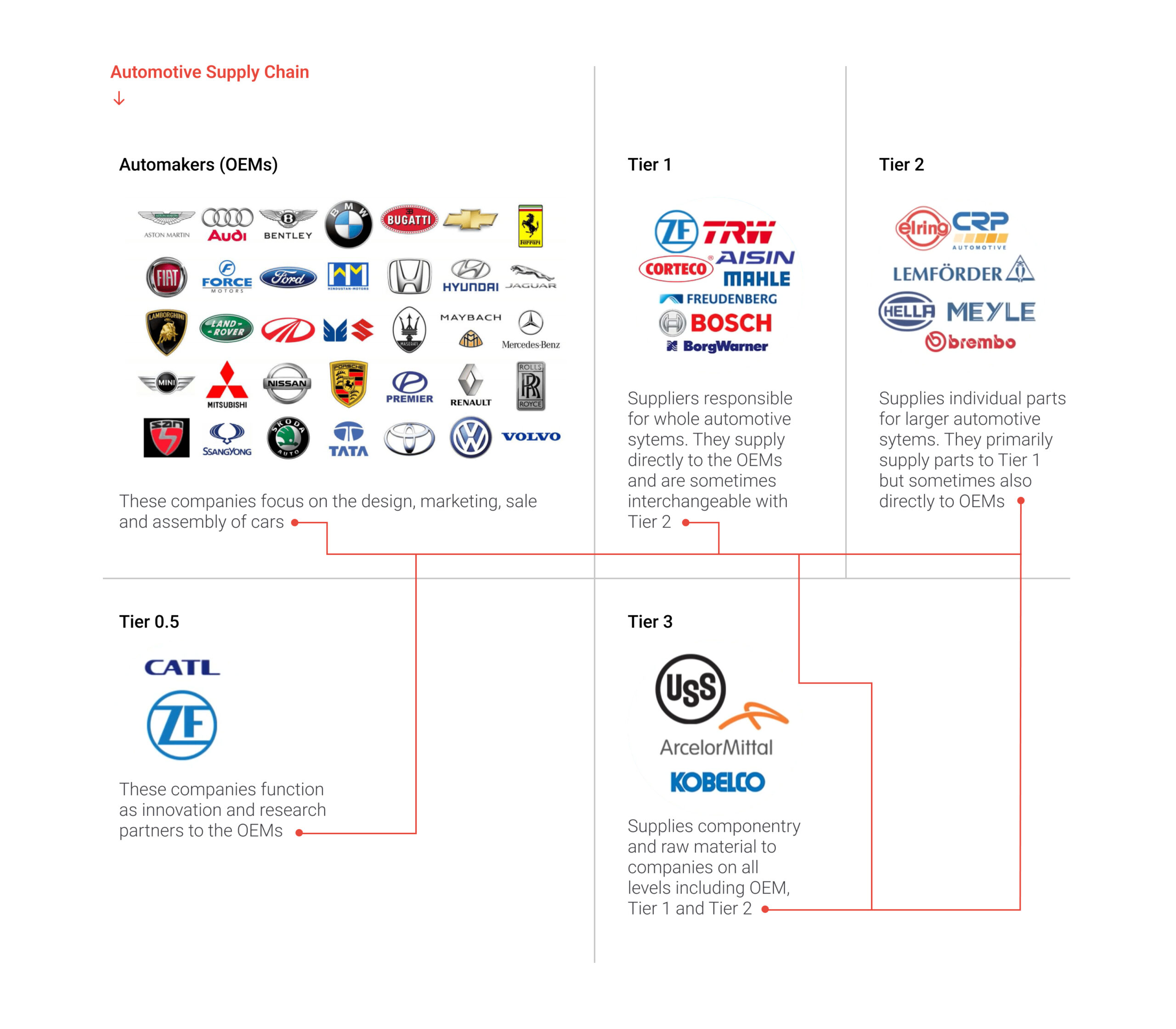
With the identification of the companies involved at various levels and their interactions with each other, clarity was achieved in mapping out the automotive supply chain. The stakeholders relevant to this case study were identified in Tier 1 and Tier 2 positions within this chain.
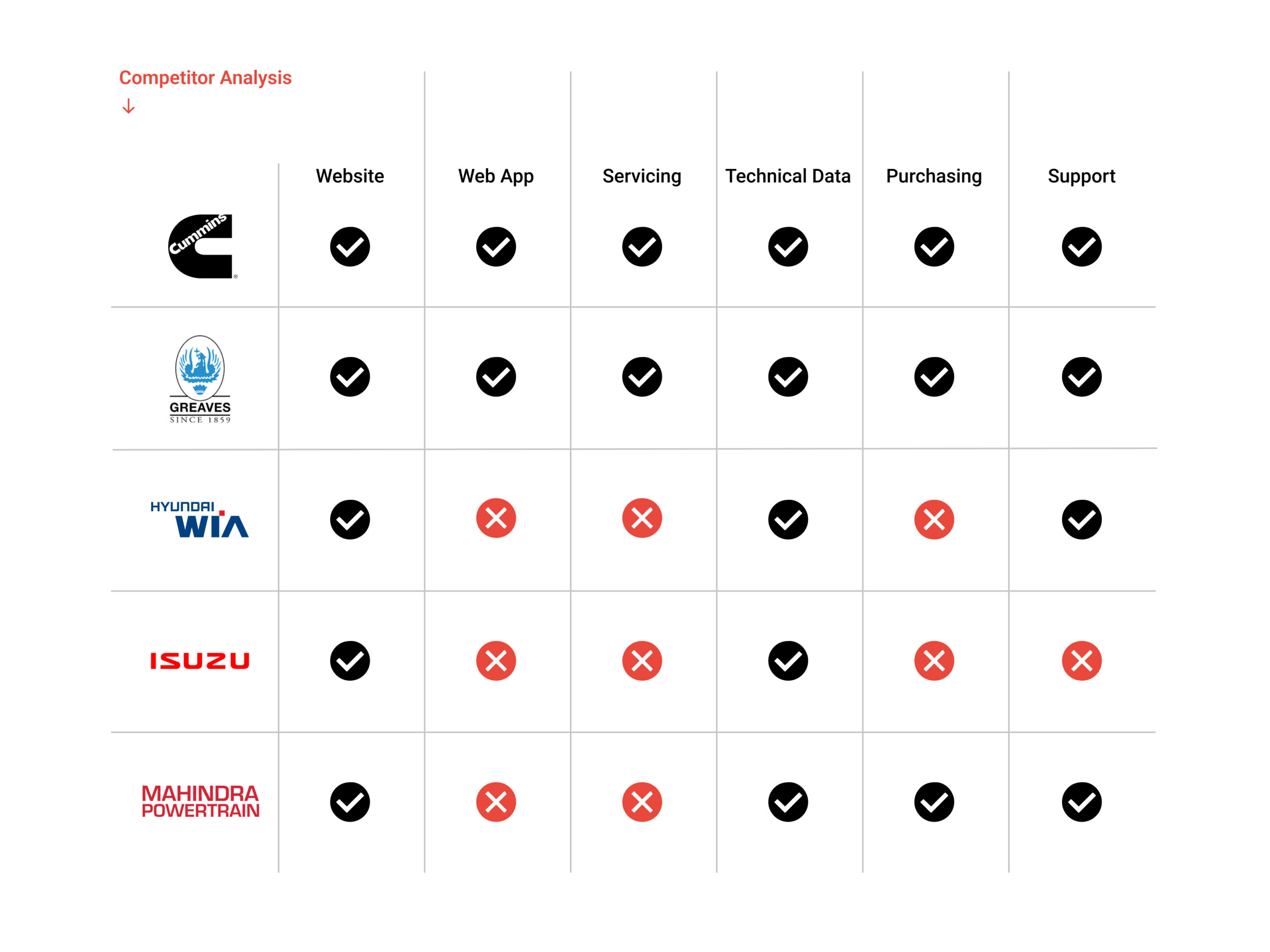
A comparative analysis of the services provided by existing diesel engine manufacturers unveiled several opportunities for intervention across various categories. Among the major players in the industry, there was a notable absence of a web application facilitating the streamlining of servicing, purchasing, and support processes, thus presenting a significant opportunity in this regard.
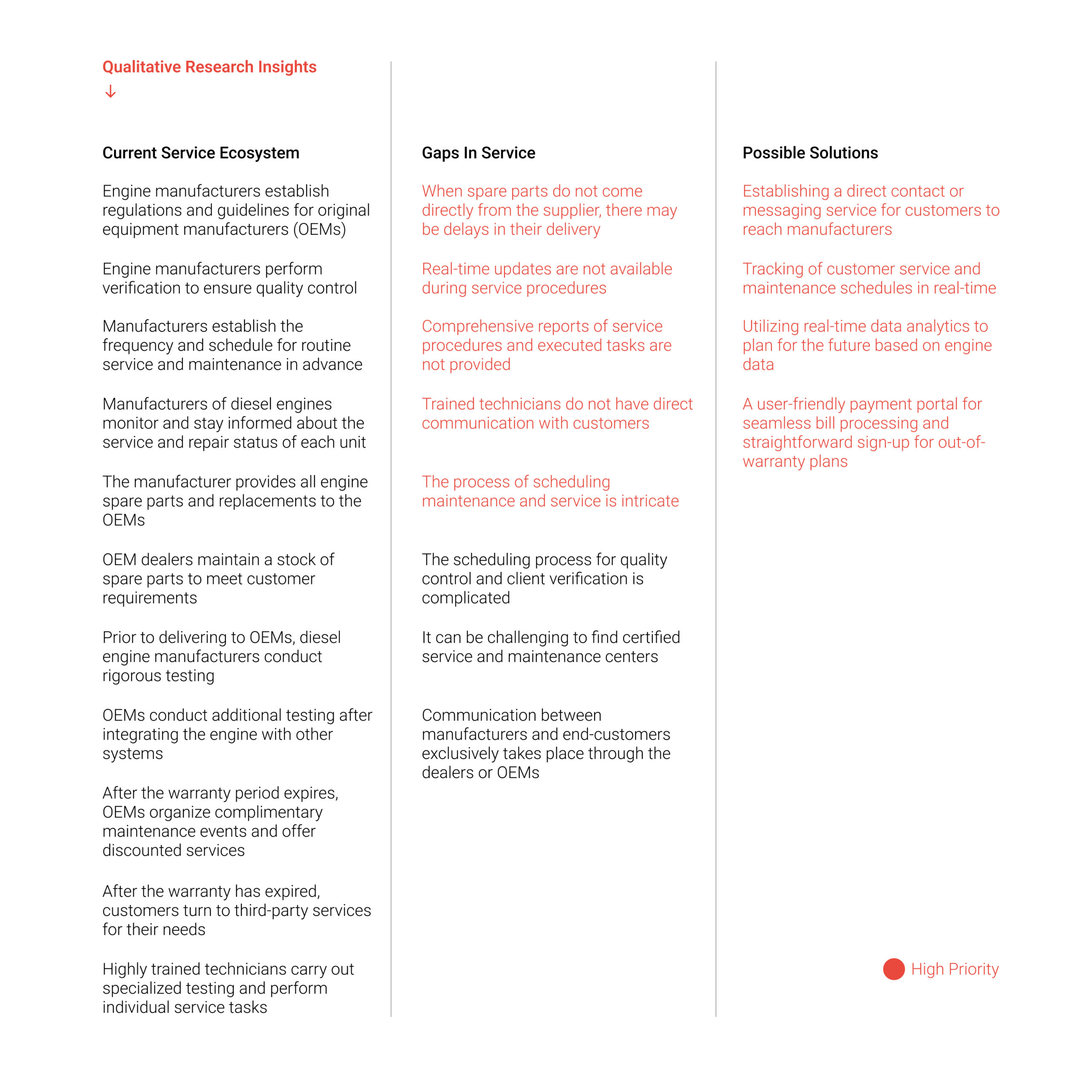
All the insights collected and data gathered were compiled into a solution checklist. Through validation with industry experts and stakeholders, a prioritized organization of potential solutions was established. These identified needs and demands within the current landscape served as the foundation for the ideation of the web application and the definition of its features.
UX Design
The development of the web app commenced with the construction of the site map, serving as the framework for the dashboard. This asset served as the foundation for adapting the application to accommodate various user groups. While unique task flows were crafted for the two user sets, they shared the same underlying style of navigation.
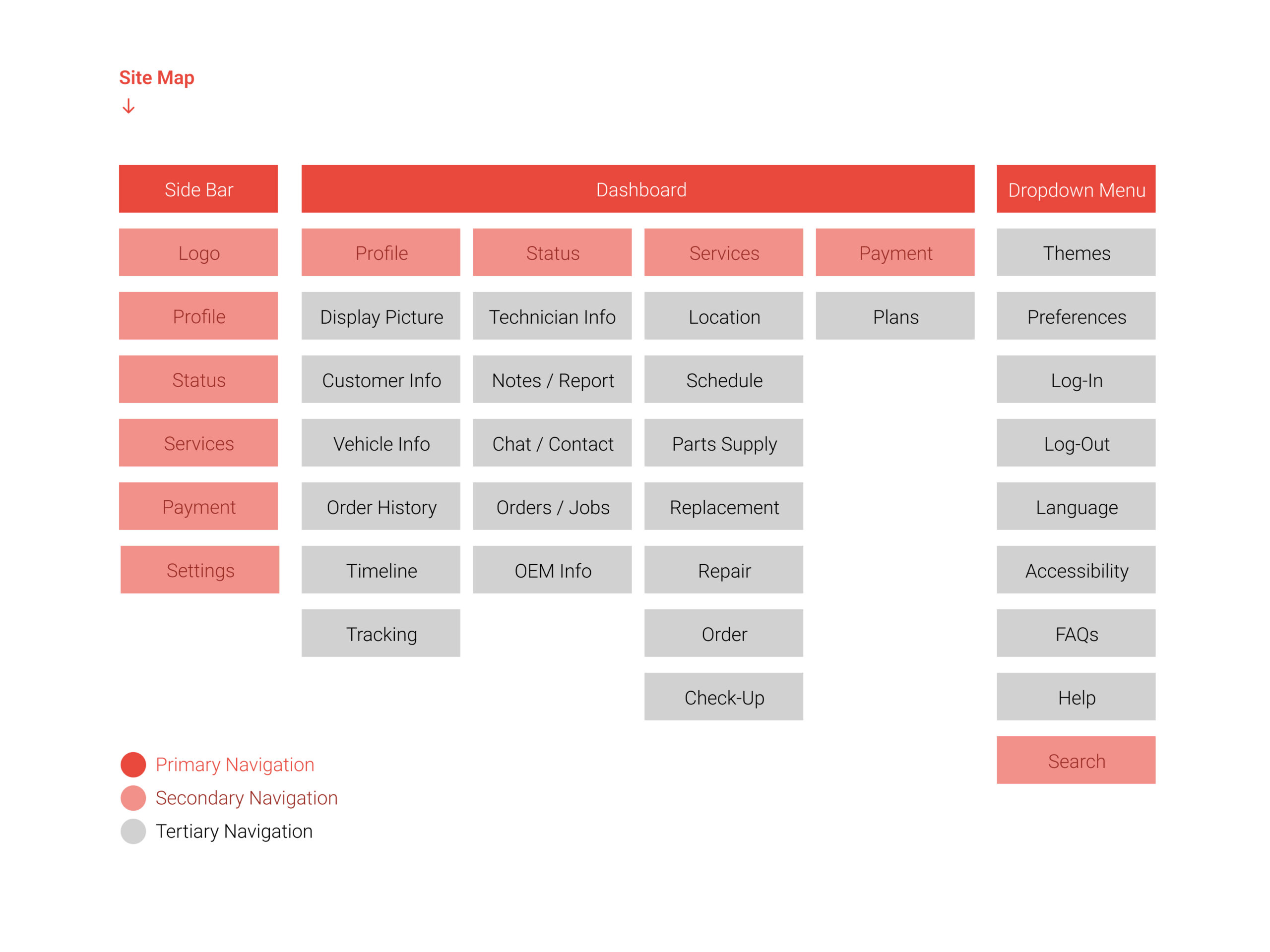
The basic navigation flows and information architecture was created by incorporating all the relevant data points and assigning hierarchy to them. The dashboard was conceived as a primarily tab-based interface, with the tabs being adjusted depending on user type due to their differing tasks and requirements within the application.
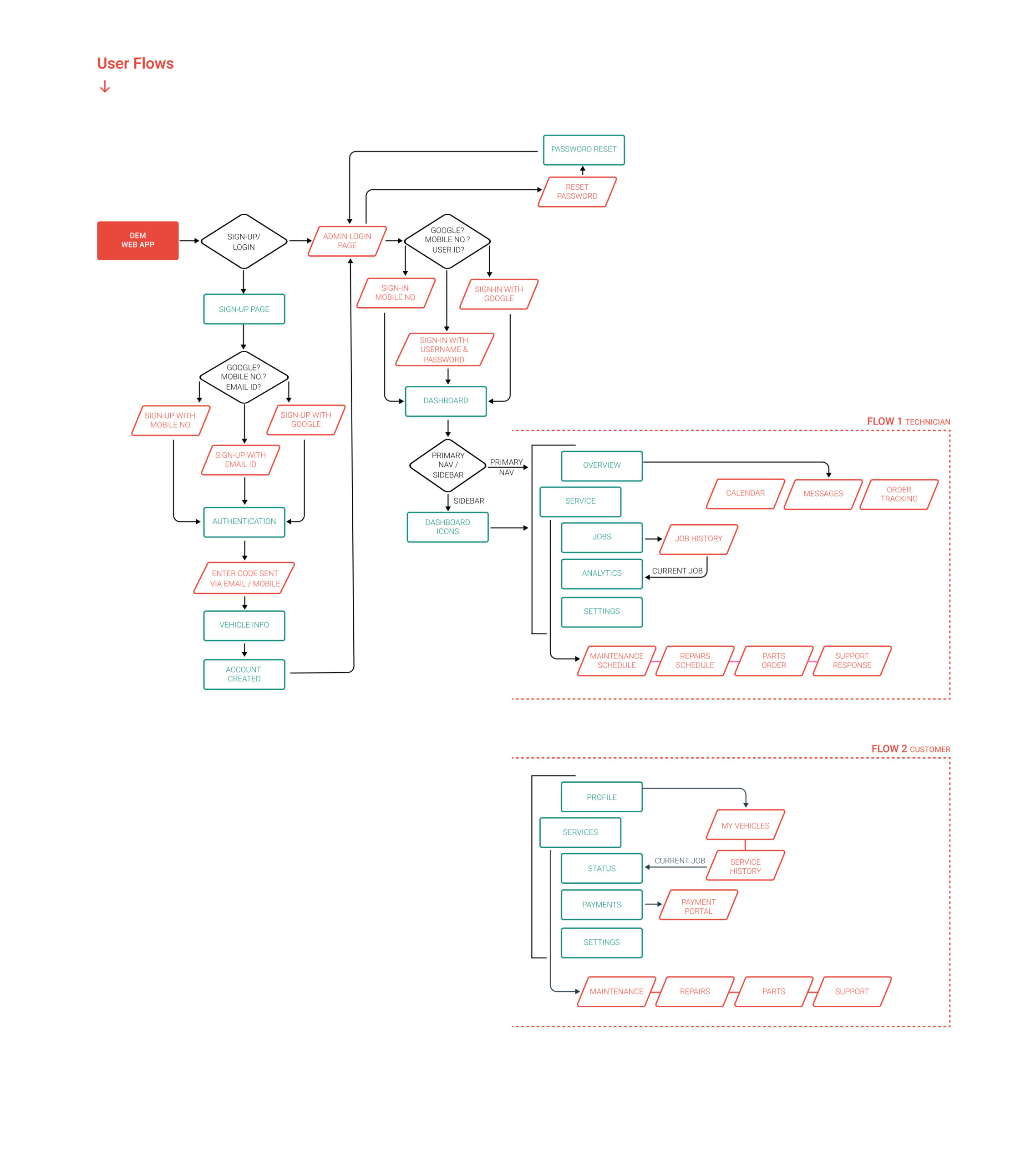
Common user flows for onboarding and application login were established. The flow branched into customer and technician pathways upon logging in, thereby enabling different users to access their respective dashboards. The researched requirements were then translated into distinct features and functionalities within the dashboard tailored for each user set.
UI Design
To achieve a user-friendly application with minimal clutter, a simplistic design was chosen, featuring a clear and concise data structure and high-contrast visual design. High-fidelity prototypes of the customer and technician dashboard interfaces were mocked up and remotely tested, eliciting positive feedback from participants.
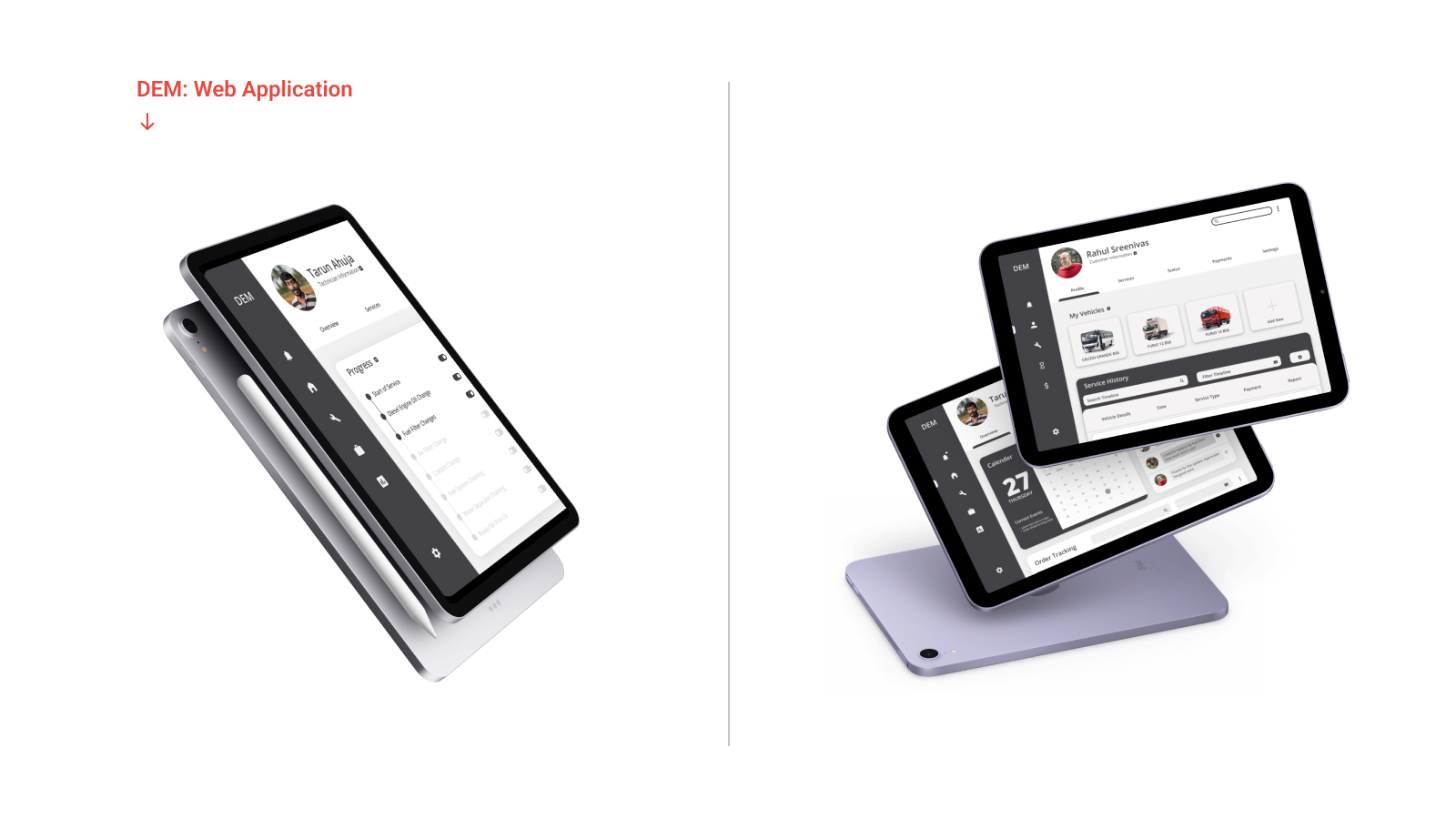
The UI was designed for technicians to use on handheld devices while carrying out service tasks and processes, enabling real-time service inputs and communication. This functionality was also extended to customers, who mainly consisted of fleet owners with multiple commercial vehicles, requiring seamless service and communication on the go. Remote accessibility was a top priority for both user sets, particularly in the context of the COVID era.
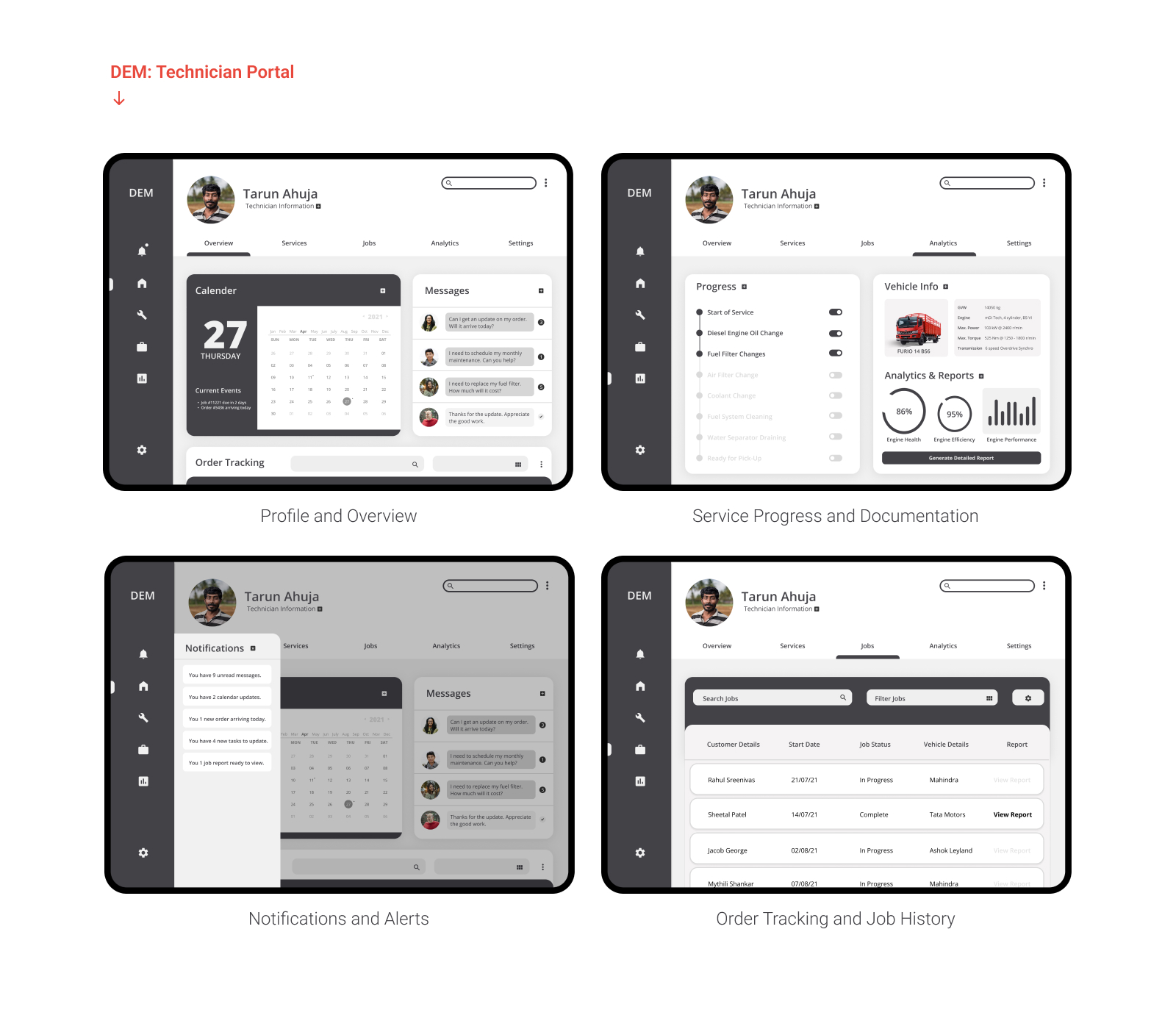
High Fidelity Clickable Prototype (Click to Test, R to Reset)
The Technician Dashboard aimed to streamline and document the servicing process. It facilitated real-time progress updates, tracked orders and jobs, managed part deliveries, generated service reports and order completion histories, and provided a direct communication channel with customers via the chat feature.
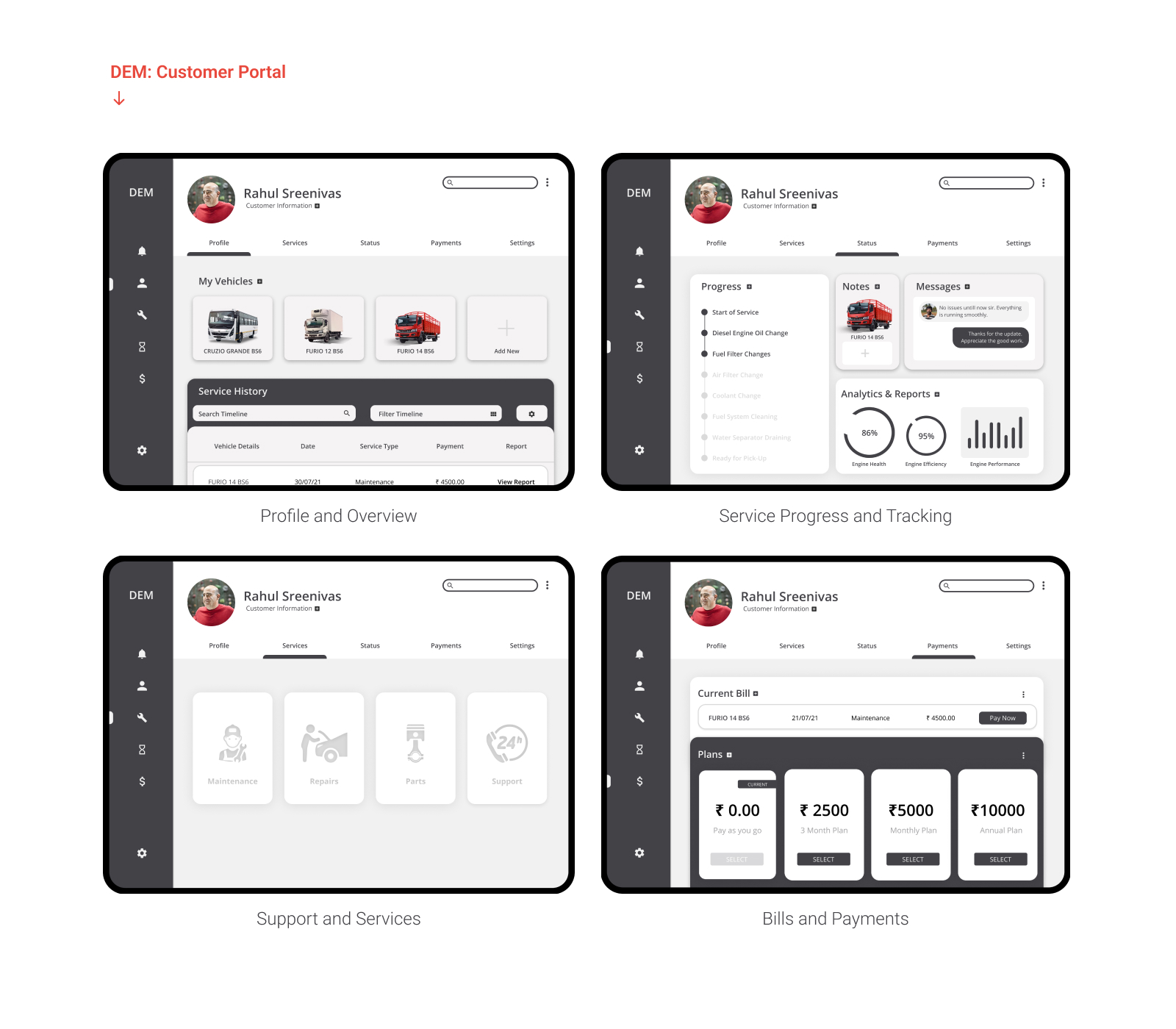
High Fidelity Clickable Prototype (Click to Test, R to Reset)
The Customer Dashboard enabled users to register vehicles, access service history, request support, order parts, view service plans, make payments, and primarily monitor real-time service progress. It also included an integrated chat feature for direct communication with technicians.
*Please visit desktop site to view clickable prototypes.